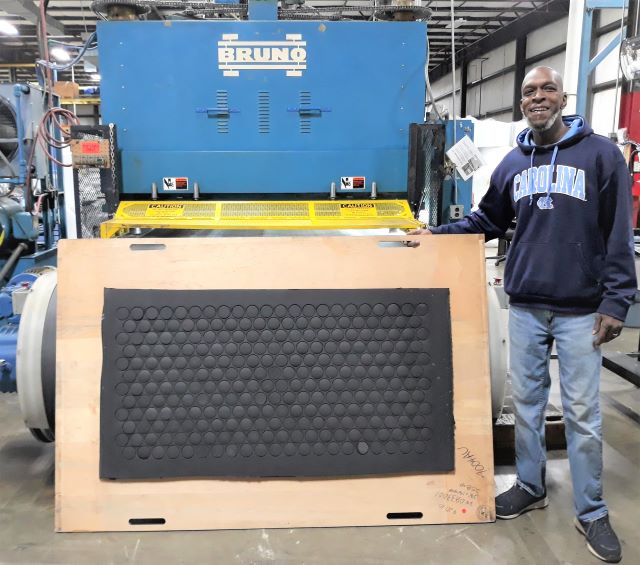
Large Format Die Cutting
CGR Products has actively been die cutting high volume parts for more than 40 years. To accommodate either very large die cut parts, or supplying parts in a prolific fashion, we use a process called “Large Format Die Cutting” Equipment CGR Products utilizes two Bruno die-cutting presses. Bruno presses are made in the USA and…
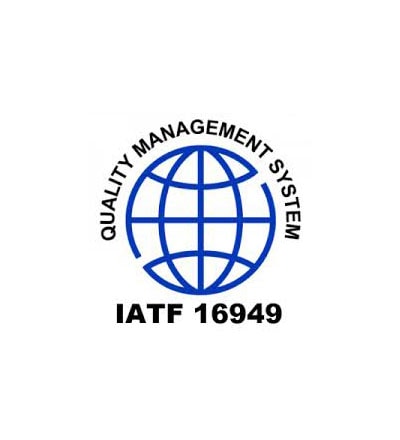
CGR Products Achieves IATF 16949 Certification
We are thrilled to announce that CGR Products, Inc. has achieved IATF 16949 certification! This prestigious certification is a testament to our unwavering commitment to quality and continuous improvement in our manufacturing processes. What is IATF 16949? IATF 16949 is an international standard for quality management systems specifically designed for the automotive industry. It sets…
Life Phases
All of us are going through different phases of life all the time and we don’t think about it, at least I haven’t, until now. I guess you think about it more as you mature (ha, ha, a diplomatic way to say “get older”). You also hear the comment from “mature” people that life flies…
Importance of Choosing the Right Gasket Material
Absolutely, choosing the right material for a gasket might seem like a minor detail in the grand scheme of things, but it holds immense importance in various industries and applications. Whether it’s in automotive engines, pipelines, or industrial machinery, the gasket plays a pivotal role in maintaining a seal between two or more surfaces, preventing…
CGR Products: Your Trusted Supplier for UL Listed Closed Cell Sponge with Adhesive
When it comes to sourcing high-quality UL listed materials for sealing and gasket applications, CGR Products stands out as a reliable partner. With a commitment to excellence and a track record of providing performance-enhancing solutions, CGR has become the preferred choice for businesses seeking UL listed closed cell sponge rubber with adhesive. What Makes CGR Products…
Choosing CGR Products for All Types of Die Cut Gaskets and Seals
CGR Products utilizes a variety of die cutting methods to produce a product that is precisely the shape and dimensions that are required. Our state-of-the-art methods can be used to cut almost any design out of soft, flexible non-metallic materials, as well as some harder and more rigid substrates. 1. Expertise and Quality Assurance CGR…
Unveiling the Top Reasons to Choose CGR Products for Your Sealing Solutions
CGR Products is renowned for its commitment to quality, expertise, and innovation in the realm of gaskets, seals, and custom fabricated sealing solutions. Choosing CGR Products as your gasket provider can be pivotal for various industries and applications. Here’s why sourcing gaskets from CGR is so crucial: Unparalleled Expertise CGR Products boasts extensive expertise in…
The “Real” You
Do you really know the “real” you? Almost everyone will emphatically say yes. So, what is the “real” you? Is it what you think of yourself or is it what others think of you? If it is who you think you are, then everyone will answer the above question, yes. People can easily list the…
Open Cell vs. Closed Cell Foam: What’s the Difference?
At CGR Products, we field a lot of questions about the differences between open and closed cell foam. To address these inquiries, we’ll be comparing the two types of foam and outlining the unique benefits and properties of each. When deciding on a material for your specific project, it’s important to understand which kind of…
Die Cut Solutions for EV Batteries using Avery Dennison Materials
CGR Products is your go-to converter of die cut flexible materials for Electric Vehicle (EV) Batteries. CGR Products provides solutions for thermal runaway, sealing out elements, heat shielding, gap fillers, battery cushioning, and more. CGR Products is a leading converter to solve challenges for EV battery manufacturers. Adhesives for Compression Pads Avery Dennison offers pressure-sensitive adhesive tapes to bond…
Interesting Times
I have been working in the converting business since 1985 and I have never seen so many external inputs converge on the industrial sector at one time and hope I never do again. It has made business planning and proactive activities, let’s just say, exciting. Distractions Covid-19 – Pandemics are obviously rare so planning for that…
Component Foams Specifically Engineered for Automakers
Guest Author: Isabell Wright, Armacell . For most major car makers, all parts must be made from materials that are on their approved source list. It’s a competitive business and only the best suppliers with a proven track record of quality, new technology, on-time delivery and service will make the cut. Once a material has…
How to Prepare for Your Next Adhesive Materials Project
Adhesive bonding is often required for projects in many applications and industries. With various types of bonds available to meet virtually any need, it’s important to know how to pinpoint the best option for your unique project. When discussing your application with a bonding products manufacturer, you will be presented with a series of questions…
Why is Being “Wrong” so Important?
Let’s face it, nobody likes to be wrong about anything. It challenges your sense of self confidence, it’s embarrassing, and it just doesn’t feel good. That said, being wrong is where learning takes place. When people are correct, they move to the next thing. There is no need for reflection or thinking. Being wrong forces people…
Ingress Protection for Electrical Enclosures
Since CGR Products’ founding in 1963, we’ve worked with design engineers to bring projects to life, and we do everything we can to make that process efficient, affordable and successful. CGR uses a wide variety of converting methods and equipment to create parts and designs with precision and efficiency Enclosure Protection Enclosure gaskets are mechanical…